What is Predictive Maintenance? How Does It Benefit Industry 4.0?
In the age of Industry 4.0, manufacturers are under increasing pressure to boost efficiency, minimize downtime, and maximize the lifespan of their equipment. One powerful strategy helping industries stay ahead is predictive maintenance. By using real-time sensor data, edge computing, and AI analytics, predictive maintenance enables smarter, faster decisions—ensuring equipment is serviced before failure occurs.
In this blog, we’ll explore what predictive maintenance is, how it compares to other maintenance strategies, and how edge computers play a key role in building intelligent, reliable, and sustainable industrial systems.
What is Predictive Maintenance?
Predictive maintenance (PdM) is a smart maintenance strategy that uses real-time data, sensors, and AI-powered analytics to predict when industrial equipment or machinery is likely to fail—so you can fix it before it breaks.
Instead of relying on routine schedules or reacting to failures, predictive maintenance helps companies take action only when maintenance is actually needed, reducing costs and preventing unexpected downtime.
Predictive Maintenance Approaches: CBM and RUL Estimation
Predictive maintenance (PdM) can be further classified into two key approaches: Condition-Based Maintenance (CBM) and Remaining Useful Life (RUL) estimation.
- Condition-Based Maintenance uses real-time data from sensors to keep an eye on equipment health. These sensors track things like temperature, vibration, or pressure. When the readings go past a safe limit, the system alerts the team to take action. This helps avoid doing maintenance too often and keeps machines running smoothly.
- Remaining Useful Life (RUL) estimation uses past data and AI to predict how much longer a machine part will last before it needs to be fixed or replaced. This lets companies schedule maintenance ahead of time, reduce sudden breakdowns, and get the most out of their equipment.
Differences Between Reactive, Preventative, and Predictive Maintenance
How does predictive maintenance differ from reactive and preventative maintenance?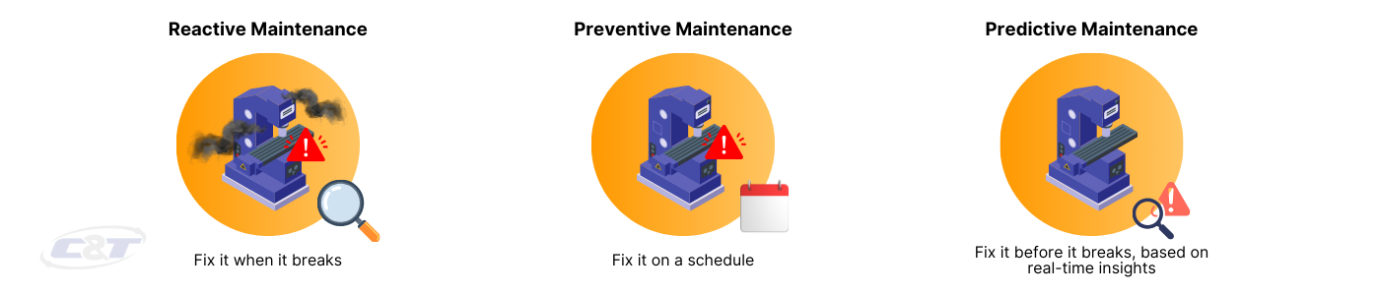
Reactive Maintenance (run-to-failure)
Reactive maintenance, also known as run-to-failure, means fixing equipment after it breaks down. It’s simple and low-cost upfront but can lead to unexpected downtime, expensive emergency repairs, and production delays. This approach is best for non-critical equipment where breakdowns don’t significantly affect operations.
Preventative Maintenance (scheduled)
Preventive maintenance involves performing maintenance on a fixed schedule, regardless of the machine’s actual condition. While it reduces the chance of sudden failures, it can also lead to unnecessary maintenance or early replacement of parts. It’s most effective for standard machinery with predictable wear patterns.
Feature | Reactive Maintenance | Preventive Maintenance | Predictive Maintenance |
---|---|---|---|
Approach | Fix after failure | Fix on a regular schedule | Fix based on data and condition |
Data Usage | None | Minimal (usage/hours) | High (real-time sensors, analytics, AI) |
Downtime Risk | High (unexpected failures) | Moderate | Low (planned actions) |
Cost Efficiency | Low (unplanned repairs, downtime) | Moderate | High (optimize maintenance timing) |
Maintenance Frequency | Unpredictable | Regular, regardless of condition | As needed, based on machine health |
Technology Requirement | None | Basic tools | Sensors, IoT, edge computing, AI |
Ideal For | Non-critical equipment | Standard machinery | Critical systems, smart factories (Industry 4.0) |
In short,
- Reactive = Fix it when it breaks
- Preventive = Fix it on a schedule
- Predictive = Fix it before it breaks, based on real-time insights
The Future of Smart Maintenance: Prescriptive Maintenance
While predictive maintenance helps you detect potential failures before they happen, prescriptive maintenance takes things a step further. It not only predicts when a failure might occur, but also recommends what actions to take, why it matters, and how to do it efficiently—sometimes even triggering automatic responses.
Predictive vs. Prescriptive Maintenance
Type | What it does | Role of AI |
---|---|---|
Predicitve Maintenance | Predicts when equipment is likely to fail, using real-time data and AI models | AI analyzes sensor data and forecasts failure timelines (e.g. Remaining Useful Life) |
Prescriptive Maintenance | Recommends or automates actions to take after predicting a failure | AI not only predicts but also suggests what to do, when, and even why—sometimes executing the action automatically |
Example:
Instead of just predicting that a conveyor belt motor will fail in 10 days, a rugged edge computer running AI models on-site analyzes temperature spikes and vibration anomalies in real time and advises:
"Schedule motor replacement in 6 days during the planned line inspection. The issue is likely caused by misalignment and heat buildup. If delayed, expect a 6-hour halt in production and increased wear on the gearbox."
Key Benefits of Predictive Maintenance in Industry 4.0
- Enhancing Smart Factory Automation
Industry 4.0 is built on automation, IoT connectivity, and AI-powered decision-making. Predictive maintenance fits perfectly into this framework by ensuring continuous equipment reliability. With edge computing and rugged industrial computers, manufacturers can implement intelligent maintenance systems that reduce downtime, boost productivity, and support fully connected smart factory operations.
- Optimizing Operational Efficiency
Predictive maintenance directly improves Overall Equipment Effectiveness (OEE) by minimizing unexpected equipment failures and maintenance-related disruptions. This leads to smoother production workflows, better use of resources, and measurable cost savings across operations.
- Supporting Sustainable Manufacturing
By performing maintenance only when needed, predictive maintenance helps reduce unnecessary part replacements, lowers energy consumption, and extends asset lifespan. These efficiencies support sustainable manufacturing practices, helping businesses meet both productivity and environmental goals.
How Does Edge Computing Enable Predictive Maintenance?
- Real-Time Data Processing
Edge computers process sensor data locally, right at the source, rather than sending it all to the cloud. This enables real-time monitoring of machine conditions like temperature, vibration, and pressure, so any anomalies can be detected instantly.
- Reduced Latency & Faster Response
Since data doesn’t have to travel to the cloud and back, edge computing reduces latency significantly. This is vital for predictive maintenance systems that need to react quickly to early warning signs before failure occurs.
- Improved Data Security & Reliability
Industrial operations often deal with sensitive or large volumes of machine data. Edge computing keeps that data on-site, improving both security and system uptime, even in environments with limited or unreliable internet connectivity.
- AI at the Edge
Modern edge computers are powerful enough to run AI and machine learning models directly on the device. This allows for on-the-spot prediction of equipment health, Remaining Useful Life (RUL) estimation, and even prescriptive recommendations—without relying on cloud infrastructure.
The Role of Industrial Computers in Predictive Maintenance
Comprehensive I/O for Sensor-Rich Environments
Equipped with broad I/O options, edge systems can connect to various industrial sensors—vibration, thermal, pressure, and more. This makes it easy to build a data-rich predictive maintenance ecosystem across diverse machine types.
AI-Driven Anomaly Detection
With AI and machine learning capabilities built in, edge computers can detect abnormal patterns—such as overheating or irregular vibration—before they escalate into failures. This supports early intervention and smarter maintenance planning.
Reliable Operation in Harsh Environments
Designed for industrial use, edge computers operate reliably in extreme conditions thanks to their fanless design, wide temperature range, and resistance to shock and vibration. This ensures uninterrupted data processing in the field.
C&T’s Featured Industrial Computers for Predictive Maintenance
-
Fanless Mini Computers for Industrial IoT Gateways
An industrial-grade alternative to NUCs. Drive real-time data telematics and analytics with fanless industrial mini computers.
-
DCO-1000-ASL Series:
DIN-Rail Fanless Embedded Computer• DIN-Rail Mounting
• Rich I/O
• Low power consumption
• Ultra-Compact Form Factor -
RCO-6000-RPL Series:
AI Edge Inference Computer• 13th/14th Gen Intel Core Processor
• 2x EDGEBoost I/O
• DDR5 RAM & PCIe 4.0 Support
• EDGEBoost Nodes (GPU/NVMe/PCIe) -
VCO-6000-RPL Series: Machine Vision Computer
• 13th/14th Gen Intel Core Processors with R680E PCH
• Blazing-Fast DDR5 with ECC Memory Support
• PCIe Gen 4 Expansion
• UL Certified
Contact us to talk with our rugged industrial experts.