Understanding 316 Stainless Steel
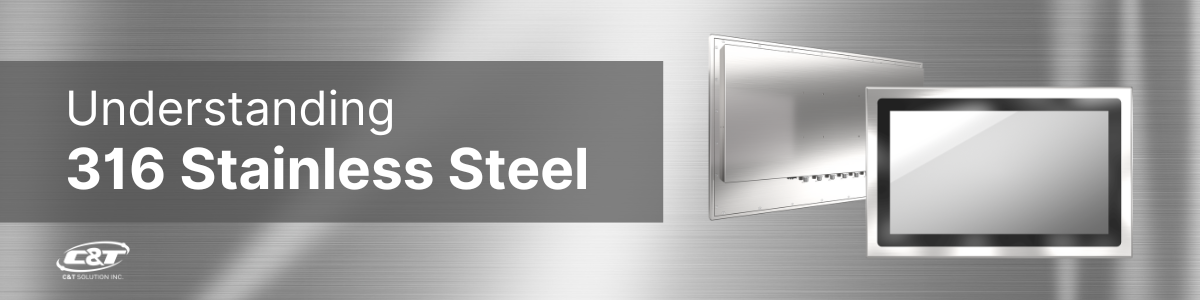
What is 316 Stainless Steel?
SUS316 stainless steel is a robust member of the austenitic family, renowned for its exceptional resistance to corrosion and remarkable durability. This grade of stainless steel primarily comprises 16-18% chromium, 10-14% nickel, and 2-3% molybdenum. The inclusion of molybdenum significantly enhances its resistance to corrosion, particularly against chlorides and acidic substances commonly found in marine environments and certain industrial chemicals.
316 Stainless Steel Properties
- Corrosion Resistance: SUS316 excels in resisting corrosion from marine atmospheres and chloride solutions, making it ideal for harsh environments.
- Heat Resistance: It can withstand high temperatures without losing structural integrity, suitable for high-heat applications.
- Mechanical Strength: SUS316 maintains excellent tensile strength and toughness, functioning well across a range of temperatures.
- Fabrication Flexibility: Known for its formability and weldability, SUS316 can be easily shaped and welded into complex configurations needed for customized applications.
How does SUS316 compare to other stainless steel grades in terms of corrosion resistance and mechanical strength?
From the graph above, we can conclude that SUS316 stands out for its superior resistance to harsh chemicals and saline environments, thanks to its excellent balance of high corrosion resistance and good mechanical strength. While other grades like 410 and 420 offer higher mechanical strength, they do not match SUS316's exceptional corrosion resistance. Additionally, grade 2205, a duplex stainless steel, also offers high corrosion resistance and greater mechanical strength than SUS316, making it another excellent choice for environments where both properties are critical. This highlights the suitability of both SUS316 and 2205 for demanding environments where durability and longevity are crucial.
Explore other stainless steel grades.
Types of 316 Stainless Steel
Type | Key Feature | Description |
---|---|---|
SUS316 | Standard | Basic type with excellent overall corrosion resistance, toughness, and temperature strength |
SUS316L | Low Carbon | Redusces carbon content to minimize carbide precipitaion during welding, enhancing corrosion resistance in welds |
SUS316H | High Carbon | Contains higher carbon content for improved high temperature strength, suitabnle for high-heat environments |
SUS316Ti | Titanium Stabilized | Includes titanium to prevent chromium carbide formation at high temperatures, increasing heat and corrosion resistance |
SUS316LN | Low Carbon, Nitrogen-Enhanced | Enhanced strength and superior pitting corrosion resistance due to added nitrogenm used in demanding environments |
SUS316F | Free-Machining | Incorporates sulfur to improve machinability; slightly lower toughness and corrosion resistance than SUS316 |
Now, which one has the most mechanical strength? Let's take a look at the graph below.
The graph of SUS316 variants shows that while all maintain excellent corrosion resistance, SUS316LN offers higher mechanical strength due to added nitrogen, making it suitable for tougher applications. SUS316F, with slightly less corrosion resistance, improves machinability for extensive machining needs. This variety ensures each variant can meet specific industrial requirements effectively.
Importance of SUS316 in Industrial Applications
SUS316 stainless steel is crucial for industries that need materials to resist rust and damage, even in tough conditions. It stands up to corrosion from chemicals and salt, making it ideal for pharmaceutical and food processing industries. Its strength holds up under both high and low temperatures, which is essential for these sectors where cleanliness is critical. SUS316 is also easy to mold and weld into specialized parts, making it very versatile for different uses. This makes it a practical choice that saves money over time due to its durability and low maintenance needs.
Explore C&T's Full IP66/69K SUS316 Washdown Touchscreen Computer
From agriculture to modern virology studies, diverse industrial sectors are embracing Industry 4.0 for improved efficiency, safety, and hygienics. In these spaces that require the utmost cleanliness, C&T’s IP66/69K rated SIO Series is an all-in-one touchscreen computer with a rich display that grants exceptional control and automation capabilities. The SIO’s remarkable suitability to hygienic environments simplifies integrations while enabling intuitive HMI, process automation and workload consolidation. Built with a sealed IP-rated SU316 stainless-steel enclosure, the SIO Series is ideal for Industry 4.0 solutions in food and beverage processing, pharmaceutical manufacturing, and cleanroom settings.
Learn more about SIO-200 Series.
FAQ
- What are the four types of stainless steel?
- Austenitic: Non-magnetic with high corrosion resistance, commonly used in both consumer products and industrial applications
- Ferritic: Magnetic with good corrosion resistance but less ductility than austenitic steels
- Martensitic: Magnetic and can be heat-treated for high strength and hardness but have lower corrosion resistance
- Duplex: Features a mixed microstructure of austenite and ferrite, offering high strength and excellent corrosion resistance
- What are stainless steel grades?
Grade | Type | Composition | Properties | Common Applications |
---|---|---|---|---|
2205 | Duplex | 22-23% Chromium, 4.5-6.5% Nickel, 3-3.5% Molybdenum | High strength, excellent corrosion resistance, especially in chloride environments | Chemical processing, oil and gas industry, marine environments |
316 | Austenitic | 16-18% Chromium, 10-14 Nickel, 2-3% Molybdenum | Superior corrosion resistance, especially against chlorides and acids | Marine applications, chemical processing, medical implants |
304 | Austenitic | 18-20% Chromium, 8-10.5% Nickel | Excellent corrosion resistance, good formability | Kitchen equipment, tanks, piping, architectural trim |
321 | Austenitic | 17-19% Chromium, 9-12% Nickel, 0.7% Titanium | Excellent resistance to intergranular corrosion | Aerospace components, expansion joints, thermal oxidizers |
440C | Martensitic | 16-18% Chromium, 0.95-1.2% Carbon | High hardness, wear resistance | Bearings, valves, high-quality knife blades |
303 | Austenitic | 17-19% Chromium, 6-10% Nickel, 0.15% Sulfur | Improved machinabilty, good corrosion resistance | Nuts, bolts, shafts, gears |
430 | Ferritic | 16-18% Chromium | Good corrosion resistance, formable, less expensive | Automotive trim, appliances, architectural applications |
409 | Ferritic | 10.5-11.75% Chromium, 0.5% Titanium | Good corrosion resistance, weldability | Automotive exhaust systems, automotive trim |
410 | Martensitic | 11.5%-13.5% Chromium | High strength, moderate corrosion resistance, can be heat treated | Cutlery, valves, kitchen utensils, dental and surgical instruments |
420 | Martensitic | 12-14% Chromium, 0.15% Carbon | Higher hardness, moderate corrosion resistance | Cutlery, surgical instruments, dental tools |
- Is 316 stainless steel magnetic?
No, SUS316 stainless steel is not magnetic. It belongs to the austenitic class of stainless steels, which are generally characterized by their high chromium and nickel content, making them non-magnetic in nature.
- 304 vs 316 stainless steel
Stainless steel grades 304 and 316 differ mainly in composition and corrosion resistance. Grade 304 contains 18-20% chromium and 8-10.5% nickel, making it highly resistant to a wide range of chemicals and corrosion, but less effective against saline and chloride exposure. Grade 316 includes an addition of 2-3% molybdenum, enhancing its resistance to chlorides and acidic chemicals, making it better suited for harsher environments like marine and chemical processing.