Making Heavy Lifting Easier: Automated Forklifts Powered by AI Edge Inference PCs
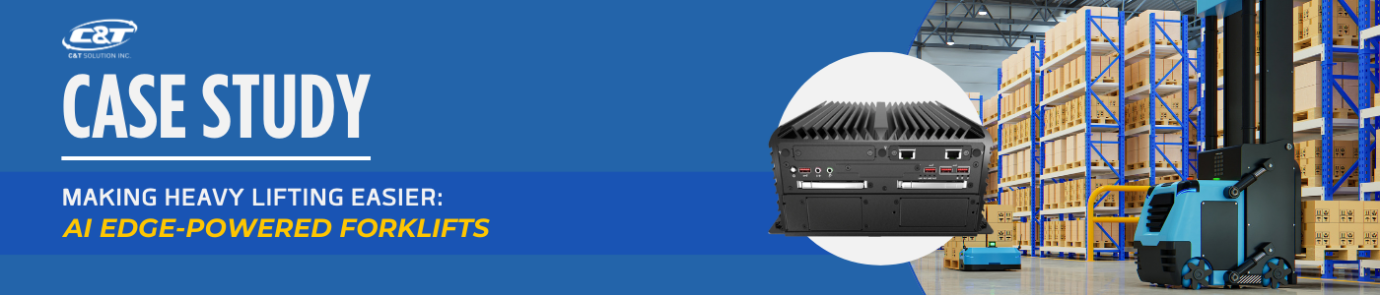
Autonomous forklifts, a mix of AGV and AMR technologies, are changing the future of warehouses, manufacturing, and logistics with advanced autonomy. These AI-driven machines have greatly improved workplace safety, made workflows more efficient, and allowed for easier scaling. This case study looks at how an automation robotics company uses C&T’s AI Edge Inference Computer to power their autonomous forklift solution.
Challenge:
- Needed a reliable edge computing solution to handle AI workloads in real-time at the edge.
- Required sufficient and compatible IoT connections to integrate all the electronics and sensors on the forklift.
- Compact design needed to fit within the already limited space of the forklift's chassis.
- Reliable performance for in-vehicle use in various warehouse conditions.
Solution:
- C&T’s RCO-6000 Series AI Edge Inference Computer (RCO-6000-CML-2).
- EDGEBoost Node with dedicated GPU support to handle AI tasks smoothly.
- Modular EDGEBoost I/O configured to support dual 10GbE LAN for fast and accurate IoT sensor data.
- Multiple connection options for essential electronics.
- Built for durability to handle tough warehouse environments.
- World-Class Certifications: UL, FCC, CE.
Benefits:
- Direct partnership with the manufacturer.
- Dedicated engineering support.
- ISO-certified facility.
Company Background
Founded in 2017 and supported by key players in the automotive and retail industries, this robotics company has focused on bringing smart automation to logistics. Their robotic forklift solution aims to improve productivity by solving common warehouse challenges like bottlenecks and inefficient material flow, while also making the workplace safer. Using advanced technology like computer vision, machine learning, and edge AI, their unmanned forklifts can move through complex warehouse layouts, avoid obstacles, and complete tasks accurately. The company’s goal is to push forward AI-powered autonomy in handling materials and pallets.
The Challenge
The automation robotics company faced ongoing problems with their previous solution, which had a design that didn’t fit well in the already tight space of the forklift. This caused issues with meeting OSHA standards, which require a clear field of view for manual operation when needed. To solve this, the company started looking for a more reliable and rugged edge computing solution for their new autonomous forklift model. They created a detailed list of the requirements that needed to be met for successful deployment.
Reliability for In-Vehicle Deployment
Because of the tough conditions and limited space in the forklift’s chassis, the robotics company needed a compact and durable edge AI computing solution for in-vehicle use. Their previous edge computer was too bulky, limiting where it could be placed inside the forklift. With the forklift operating in different warehouse environments, the new computer needed to handle constant shock, vibration, temperature changes, and be maintenance-free for long-term reliability.
AI Performance for Computer Vision
A key requirement was for the industrial computer to run their autonomous AI software smoothly, without slowdowns or overheating. Since the computer is installed on the forklift, power efficiency, thermal control, and durability were important factors in choosing the right performance hardware. While a high-performance GPU could power the AI tasks, it wasn’t suitable for the forklift due to space, heat management, and sensor connection limitations. The company needed expert help to find the right performance hardware that could deliver strong AI capabilities while being rugged enough for edge computing.
High-Speed IoT Connectivity and Data Transfer
The autonomous forklift relies on multiple IoT sensors to map and navigate the warehouse. These sensors use different types of connections, including older COM ports, high-speed USB, and LAN ports. The forklift also uses high-bandwidth LiDAR sensors for precise mapping, which requires a 10GbE connection. The industrial computer needed to have enough I/O options and be compatible with all the different sensor connections.
The Solution
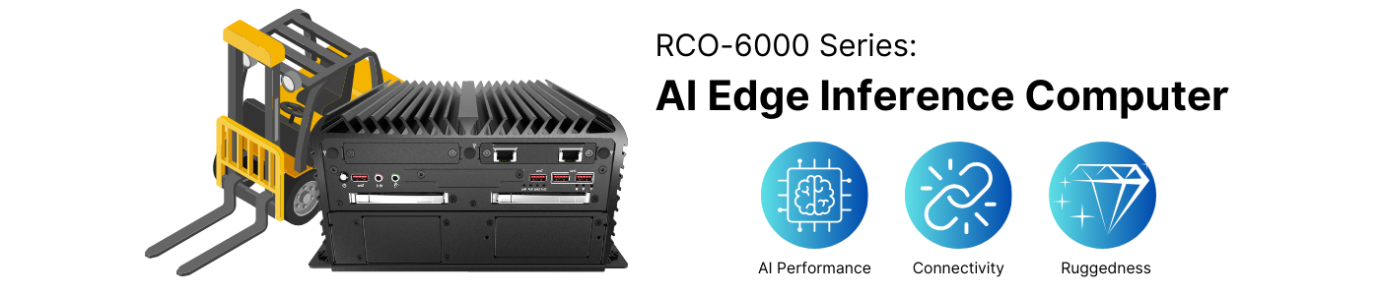
After carefully reviewing the robotics company’s needs, C&T’s RCO-6000 Series AI Edge Inference Computer was chosen as the best solution to power the autonomous forklift with computer vision. This model had already been successfully used in other autonomous applications, like self-driving delivery trucks, that also rely on computer vision and IoT sensors. With its EDGEBoost technology, flexible I/O connections, and customizable performance, the RCO-6000 Series offered an optimized edge computing solution for AI-powered forklifts used in warehouses and logistics centers across North America.
Real-Time AI Performance with EDGEBoost Nodes
To support the autonomous forklift’s AI software, the computer needed to balance performance, size, and durability. Using modular EDGEBoost Node technology, the RCO-6000 Series could be configured with a low-profile GPU, the RTX A2000, chosen for its AI processing power, compact size, and energy efficiency.
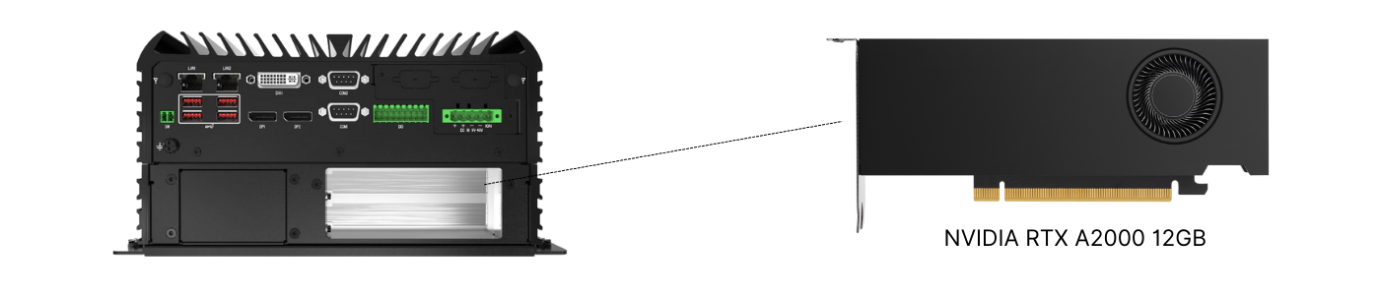
This gave the computer the ability to handle AI workloads while being tough enough for in-vehicle use.
NVIDIA RTX A2000 | |
---|---|
GPU Memory | 12GB GDDR6 with ECC |
Max Power Consumption | 70W |
Form Factor | Low-profile Dual Slot |
Easy IoT Connectivity with EDGEBoost I/O Technology
The RCO-6000 Series offers many built-in IoT connection options and can be further customized with modular EDGEBoost I/O technology. The onboard I/O supports various IoT connections like COM, USB, LAN, and isolated DIO. For the autonomous forklift, which uses a LiDAR sensor requiring a 10GbE connection, C&T configured the RCO-6000 Series with a dual 10GbE EDGEBoost I/O module to meet this specific need.
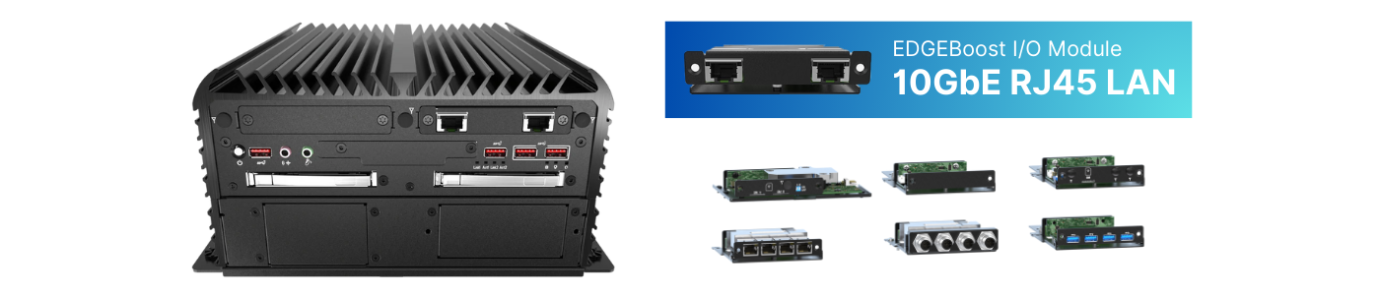
Long-Term Product Support
In addition to strong AI performance, C&T equipped the RCO-6000 Series with a 10th Gen Intel TE processor, which comes with Intel’s 10-year embedded support plan. This ensures the robotics company can rely on the same edge computing setup for a long time, without worrying about sudden hardware changes.
Durability for In-Vehicle Use
The RCO-6000 Series was built to handle tough environments and 24/7 in-vehicle use. Its fanless and cableless design prevents dust and debris from getting inside, while offering features like:
- Wide temperature range (-25°C to 70°C)
- Shock and vibration resistance (MIL-STD-810G)
- Wide power input range (9~48VDC)
- Power protection (OCP, OVP, RPP)
- Power ignition management
- CAN Bus support
- World-class certifications: UL, FCC, CE
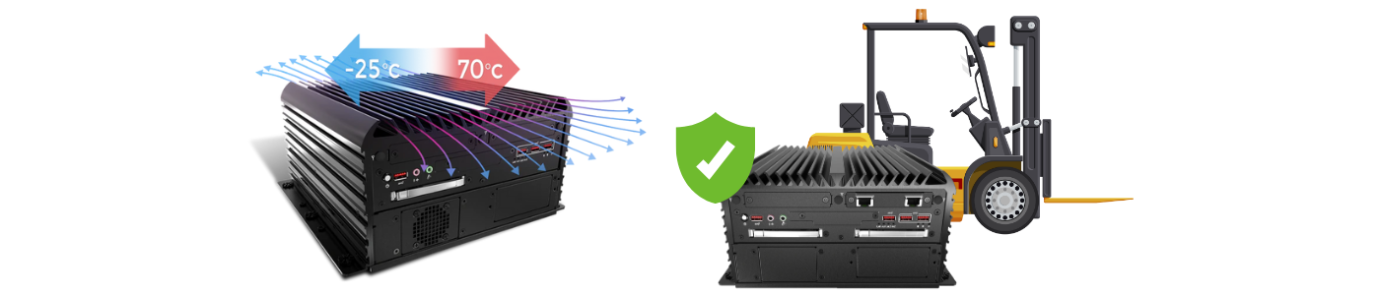
Compact Form Factor for Forklifts
The RCO-6000 Series was the smallest option compared to other edge computing devices, fitting easily into the forklift chassis without interfering with other electronics or stopping the enclosure door from closing. This allowed the company to meet OSHA standards, which wasn’t possible with their previous solution.
C&T's RCO-6000 series now supports 14th Gen Intel® Core™ processors. Explore RCO-6000-RPL.
The Benefits
C&T not only delivered a rugged edge computing solution that met all of the robotics company’s needs but also offered extra advantages as an official partner. As the direct manufacturer, C&T provided added value with top-tier engineering, supply chain management, and full-service manufacturing, which are often hard to find with overseas competitors who have limited presence in the U.S.
Direct Partnership with the Manufacturer
By working directly with C&T, the robotics company gained access to over 15 years of edge computing expertise. C&T supported them with supply chain management and technical engineering, allowing the robotics company to rely on proven computing experience and standard solutions. This helped them avoid spending extra resources or facing delays that might come with other vendors.
Responsive Sales & Engineering Support
C&T’s sales and engineering teams provided outstanding support, ensuring the edge computer not only met but exceeded the client’s expectations. When the robotics company needed custom software changes, C&T’s BIOS engineers quickly stepped in to help them configure and optimize the AI software with ease.
Localized Supply Chain Management
Thanks to our partner in the U.S., C&T's supply chain team is skilled in navigating disruptions and making quick decisions to ensure products are delivered on time. This allows for a just-in-time delivery approach tailored to the client’s OEM computing needs, ensuring smooth operations and consistent supply management.