知识中心
27.Apr.2020
Industrial PC Designs for Machine Vision Automation and Inspection
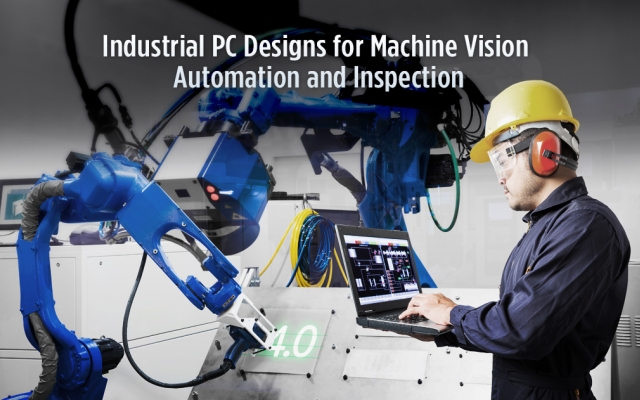
- Latest USB interfaces and GPIO to provide higher speed data transfer
- Supports multi-core accelerators for inference analysis
- Supports Wide Temperature and Wide-Voltage Spikes in harsh factory environments
- Large solid-state storage capacity to keep data in place
- Up to 64GB of DDR4 SODIMM Memory Ram for multi-tasking
- Support for latest high-speed vision cameras (GigE and USB 3.0)
- Modular PCIe Expansion slots for high performance GPU accelerators
How Machine Vision is a Step toward Machine Learning?
Machine vision, also known as the eyes of a machine, refers to the ability of a computer to see using one or more video cameras. It captures images, process them and creates an action course. Although these steps sound time-consuming, it is done at the speed of light. The only time-taking process is the gathering of data, although this process has been faster with more advanced AI. The machines combine hardware and software algorithms to process complex visual tasks that the human eye cannot process. Their most prominent configuration includes programmed sensors, software (algorithms that can identify patterns) and computing power (CPU and GPU) capable of analyzing images at high speed intervals. Faster computational power in x86 processors and powerful real-time graphics accelerators allow for industrial PC machines to provide results faster and more accurate results in comparison to humans. This is incredibly relevant when looking at use-cases for robotic automation because of the enormous about of productivity and efficiency gains with intelligent machines.Technological advances have resulted in more efficient cameras and computers capable of replacing the human eye. Businesses rely on using industrial pc for machine vision to improve quality, efficiency and operations. Although having a 20/20 vision score is a plus, the human eyesight is far less effective than the machine vision due to many variables like fatigue. The 20/20 reference only suggests that a human is able to decipher a chart from 20 feet away in normal light conditions. However, machines can see more precise and detailed for longer periods of time without needing any rest. Video cameras can be sensitive to a range of wavelengths wider that the human eye. Some industrial computers for machine vision are used to see infrared, ultraviolet and x-ray wavelengths that are useful under weaker light conditions. For example, this can be extremely important in an automation factory in harsh conditions with low lighting, where inspection or picking is mission-critical.
Many manufacturers use automated machine vision instead of human inspectors because it is better suited to repetitive inspection tasks. It is faster, more objective, and works continuously. Machine vision systems can inspect hundreds or even thousands of parts per minute and provides more consistent and reliable inspection results than human inspectors. Their ability to work 24/7 and collect and store large amounts of data increases efficiency and accuracy. Eventually, there will be enough data that will allow the machine to proceed independently per trained algorithmic models.
8 Key Features When Designing an Industrial PC with a GPU for an Inspection Machine
1. USB 3.0 input / output for high-speed IoT sensors
USB 3.0 has put a major footstep in the industrial, medical and mass production application. This interface has become the official standard in the image processing and machine vision industry, also known as USB3 Vision Standard. This standard has been created with more uniform rules that prevents incompatibility with certain accessories and proprietary solutions.Machine vision uses one or multiple cameras to inspect and analyze objects. The data obtained from these cameras are then transferred to an industrial pc for processing and analyzing. The size of the data depends on the quality of the camera. As the quality increases, the size and amount of data increases as well. For this reason, the data needs to go through a faster interface in order to detect and process information at a fast pace. C&T’s industrial computers are equipped with the latest USB 3.0 standards, providing up to 5Gb of data per second, which is 10 times faster than USB 2.0 and provide easy plug and play integration.
2. General purpose Input/output (GPIO) digital signal interface
Many high-precision applications require that cameras capture a frame at an exact and precise moment. This task seems easy when one object is moving at a slightly slow pace. However, having multiple cameras detecting multiple objects at the speed of a train can be daunting. Every camera must take the frames simultaneously.To make this task possible, C&T’s Machine Vision computers are equipped with a GPIO interface that can output an inputs and output mechanisms are triggered, it can request the device that certain actions be performed. By connecting these cameras to the industrial pc GPIO, the device action or trigger can be controlled with a programmable software.
3. Supports x16 PCIe Gen3 GPUs for real-time inference
Besides having high-quality cameras, a machine vision computer uses a dedicated GPU to process all the data that comes in. The CPU in combination with a GPU play equally important roles to balance specific workloads defined in the inference algorithm. With so many types of GPUs in the market, one advantage that C&T’s industrial pc with GPU offers is the flexibility of using both low-powered GPUs and high CUDA core GPUs like a GTX 1050 Ti, with 768 cores. For example, some vision application workloads require more power, and some require a less demanding GPU utilization and therefore help reduce overall costs. But it’s important to highlight that many machine learning algorithms using visions rely on robust performance accelerators like a GPU for real-time computing parallelism. This basically allows computers and machines to process in real-time and make decisions immediately rather than sequentially. Many robotics and automation applications use industrial pc with added GPU accelerators to help identify and pick objects using visions technology. Read more about inference analysis and how it work with GPU computers.4. Up to 4x High-Capacity SATA SSDs for Data Redundancy
We are in an era where AI is creating new ways of analyzing data. Ideally, having unlimited storage would provide more accurate results, but this is costly and often reserved for the centralized cloud. For example, the RCO-6000 & VCO-6000 industrial pc for machine vision can be equipped with up to four, latest generation, SATA-III solid state drives (SSD) up to 8TBs each; this allows for a max storage capacity of 32TB. While not unlimited storage, it allows the machine to store an enormous amount of data aggregated in vision applications. In addition, these industrial computers can run RAID options to ensure data redundancy.5. Extended Operating Temperature for Harsh Environment
As machines work tirelessly to accomplish our objectives, one important factor to consider is the heat dissipation generated by it. Since GPUs generate a vast amount of heat, electrical components’ worst enemy, C&T’s Industrial pc with GPU support has been validated to ensure reliability with its aluminum heatsink chassis to accomplish fast heat dissipation. This is achieved through the unit’s unique heat sink design, allowing it to work in temperatures ranging from as low as -25°C up to 60°C. The key engineering challenge is to balance the high power input from GPU and maintain an industrial thermal design to ensure longevity.Along the GPU and CPU, it is crucial that machine vision application possesses enough memory to hold and work with large datasets. Having enough memory RAM allows more space to process volatile data in real-time. C&T’s Industrial Computers holds up to two DDR4 SODIMM slots, which provides higher clock speeds to achieve faster transfer rates. Memory RAM is often compared to the size of a person’s working space; the bigger the desk the more space it will have to multitask.
7. Data Encryption and Security: Trusted Platform Module (TPM)
As digital IoT applications communicate from machine to machine, it’s important to understand data privacy and security. Industrial pc with GPU accelerators are equipped with the latest TPM 2.0 chip, a dedicated microcontroller that enhances computer security and privacy on the hardware-level. Compared to its older version (TPM 1.2), TPM 2.0 offers better computer security by hosting more algorithms and security features. Read more about TPM technology and features for industrial computers here. It includes software and hardware security mechanisms to allow for hardware encryptions. For instance, if an SSD is removed from the system, the hardware cannot be read anywhere else but the original computer. Or, if the system has been compromised by a virus or a malware, the unit will try to boot on quarantine mode in order to fix the issue.8. Support for GigE Cameras
For the past couple of years, we have seen more devices being connected wirelessly thanks to wireless interfaces such as Wi-Fi, Cellular/LTE, Bluetooth, GPS and many more. We have also seen a big improvement with wireless HD Cameras. However, this wireless interface still needs more improvement in order be more reliable and to process and transfer larger volumes of data. Currently, the most popular wired interface for HD cameras is still USB, but it has cable length limitations. This is an issue when applied to a variety of long-range applications such as factory automation vision guided robotics.To eliminate speed and distance barriers, many camera manufacturers have found a new standard to connect cameras to the PC: GigE Vision Standard. This standard was adopted in 2006 by using the GigE interface for industrial imaging processing. While not offering faster transfer speeds than the USB 3.0 interface (up to 5Gb/s), it can be connected from distances of up to 100 meters (approximately 328 feet). It also reduces costs as it does not require image processing cards such as frame grabbers which, in some way, are expensive. Moreover, GigE interfaces allows easier and faster combination of multiple cameras.
Other Industrial PC Use Cases for Machine Vision Technology
Machine vision has made a huge impact on factories and industries that require quality inspection, inventory sorting, etc. But, the eyes of a machine can perform more complex tasks related to safety. All humans must do is teach the unit what it needs to identify and perform. Eventually, with enough information, the system can replace the human workforce. For example, nowadays, more countries are relying on machine vision surveillance to increase public safety with rugged NVR computers. In the past, first responders had to check an entire video clip to look for their targets. However, police nowadays take advantage of the system’s ability to detect and recognize people and identify potential suspects and prevent crimes through powerful inference algorithms. Although this technology is expensive and in its early stages, machine vision will eventually contribute to a safer community.Machine vision has also made a huge impact in the automotive industry, reducing the number of accidents and deadly casualties (nearly 1.35 million people die in road accidents per year, 3,700 deaths a day). Most vehicles nowadays use multiple radar sensors and cameras to observe the road and driver behaviors in order to collect data and use algorithms to detect driving patterns. Vehicles are equipped with high-processing machine visions that can track and make decisions live.
More advanced vehicles integrate cameras and special detection systems such as LIDAR, which stands for Light Detection and Ranging. A remote sensing method that uses light in the form of a pulsed laser to measure ranges. The system sends thousands of laser pulses every second to detect surrounding objects and reflect back. It creates a 3D point cloud and records each reflection creating an animated representation. It helps vehicles keep a safe distance from other vehicles, spot roadblocks and other obstructions ahead, and prevents accidents as a result of human negligence.
Airports have also been increasing their security and performance by installing advanced machine vision systems all over the airport. These systems center arounds improved security screening of passengers and luggage. Eventually, cameras will be able to scan and recognize passengers without any travel documents. Besides facial recognition, more advanced airports monitor ground operations to tracks potential problems and delays. Airplanes need time to land and taxi, unload and load passengers and luggage, fuel, etc. Machine vision tracks every process in order to be more efficient.